What is Pressing?
The pressing process removes creases and wrinkles from the garments and the outlook of the garments is improved as well as pressing. The fine appearance of final garments is mostly influenced by the pressing process, which makes them more appealing.
To shape semi-finished garment panels and finished garments, finishing and pressing machines first bring down the fabric’s fibers to an elastic condition, after which they extend and set.
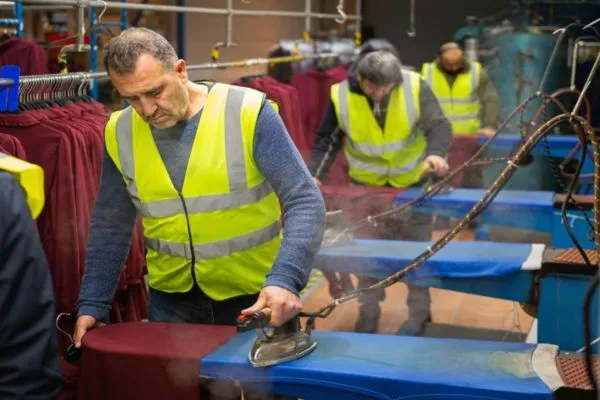
Pressing or ironing is done by treating a cloth to heat and pressure with or without steam to impart a flat appearance to the garments. It is the most important finishing process in the ready-made garment sector. There remains a separate section for ironing the products In apparel industries. Heated plates and electric irons in moist conditions are needed for the garments.
Objects of Pressing:
Pressing or ironing has several objectives which are given below:
- Removing unwanted creases and wrinkles,
- Application of heat transfers
- Shaping the garments
- To apply the necessary crease,
- Under pressing,
- Final pressing.
- Set seams and hems.
Types and Methods
There are different types of pressing used in garment manufacturing, each with its own purpose and technique. Here are some of the typical types:
- Under pressing: is the pressing operation done on garment components as they are assembled.
- Hand pressing: This is done manually by using a traditional iron and pressing board. It’s applicable for detailed areas, delicate fabrics, or for pressing a single seam at a time.
- Form pressing: A specialized press with a shaped form is used here to achieve specific shapes, like cuffs, collars, or pockets. Heat and pressure are applied to create a crisp, finished look.
- Top pressing or final pressing is the final finishing operation after sewing in which a garment undergoes treatment after being completely assembled. This technique uses a flat pressing surface with heat and steam to press the entire garment
- Unit pressing: The technique uses multiple functions, like steam, heat, and vacuum, to press specific garment areas. It’s frequently used for pressing pockets, collars, and sleeves.
- Fused pressing: A fusible web material is formed by fused pressing that bonds two pieces of fabric together. It’s often used for creating hems, collars, and waistbands.
Here are some additional points to consider before applying:
- The heat settings and pressure usually depend on the fabric type.
- To protect the fabric’s outer surface, pressing is often done on the inside of the garment.
- Pressing cloths and pressing hams can be useful for applying to certain fabrics and areas.
Basic Pressing Components:
- Heat: Heat is common in most pressing operations to soften the fibers while stabilizing the garment shape. Temperature selection is crucial, as an incorrect temperature setting can severely damage fibers and yarns.
- Moisture: steam generates moisture. Steam at different pressures has variable moisture content. The higher the supply of steam pressure, the lower the moisture in the steam. The presence of moisture adversely helps fiber swelling properties and thus shape stabilization. The amount of moisture also depends on fiber types. Natural fibers like cotton and wool and regenerated cellulose fibers such as bamboo viscose and viscose rayon require the presence of a proper amount of moisture in the steam. On the other hand, synthetic fibers mostly require heat to aid in swelling and, therefore, relaxation of the fabric structure. High amounts of moisture may cause unwanted fabric shrinkage and color bleeding, which causes great loss in the industry.
- Pressure: Pressure is applied to the garment during pressing to maintain more suitable crease retention and permanency. Excessive pressure may cause garment or crease distortion
- Vacuum: Vacuum is applied at the end of the pressing action. Vacuum mainly draws cool air through the garment to lessen the garment temperature and lower the moisture content. This process also increases shape retention. This is particularly relevant for garments made of wool or wool blends, but it also applies to cotton and viscose blends with synthetic fibers like polyester and nylon.
- Drying: Following the steam and pressure application on the fabric, the finished garment must be dried and cooled so that the fabric can return to its regular moisture content in a steady condition. using a vacuum action to remove the excess water from the fabric while also cooling it.
- Time: Depending on the type of fabric being pressed, there will be an ideal amount of time for each component to be exposed to steam, pressure, and drying.
Various Pressing Machinery
Steam press/bucket press:
Steam presses consist of two things: a static buck and a head of complementary shape closing onto it, thereby the garments being sandwiched by the press. A frame housing the buck has a round shape for pressing different garments and linkages to close the head by applying a scissor action. Steam is passed to the head and buck through a pipe system. A vacuum is created by a vacuum system to provide suction through the buck. It should be confirmed that the garment is not damp or distorted after pressing. Various types of presses have been used in steam pressing, such as the collar press, sleeve press, shoulder press, back and front press, and collar master.
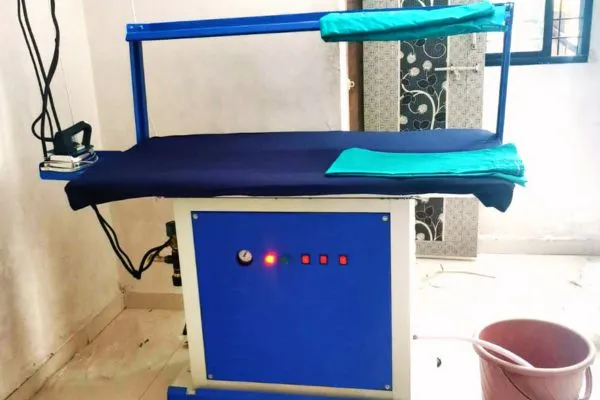
Carousel Press:
The carousel press is a comparatively new pressing operation in which a pair of bucks is rotated between the operator and the head. The head can be either single or double based on the buck being identical, or an opposite pair for pressing the left and right of a garment part. Scissor action and vertically acting heads can be noticeable in this press.
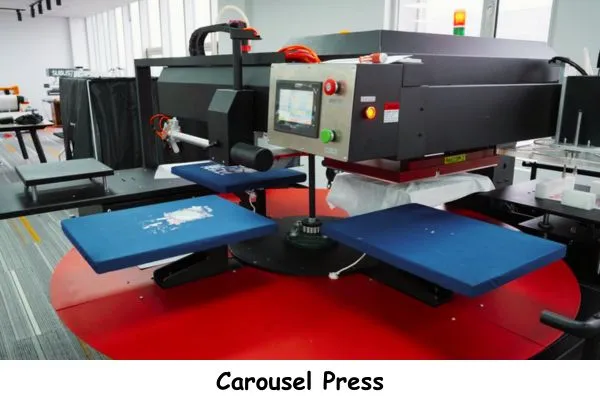
Trouser Pressing:
Jeans, women’s trousers with simpler construction that need a less sharp crease, men’s trousers including four pockets, and suit trousers including a wide variety of garments are being finished by trouser pressing. The trouser press is carried out in two operations. The initial operation for leggings is done on a flat press to set and crease the legs, followed by a sequence of lays around the top of the trouser on a contoured press.
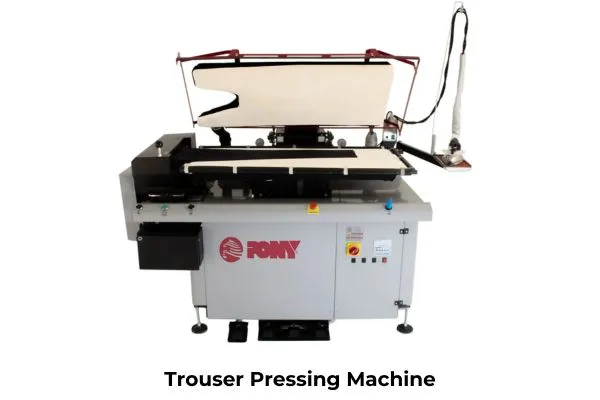
Double-legged-pressing Machine
These machines have vertically acting heads, carousels, and microprocessor controls. Additionally, steam presses are covered by heat-resistant silicone foam, and tables are used with irons and vacuum boards. outside of the steam presses is covered with a woven polyester cover. Sometimes stretch nylon is highly required for the contoured bucks.

Steam Finisher:
This finisher is widely known as a form press or a ‘dolly’ press. It includes a compressed air system, a frame for a steam distribution system, and a pressing form developed of a canvas bag in the proper silhouette for the garment to be pressed.
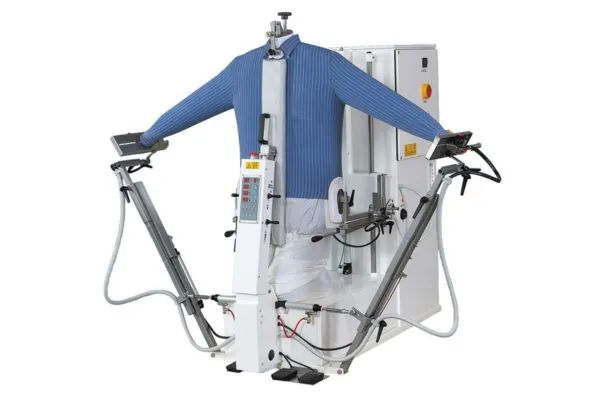
Tunnel Finisher:
Tunnel finishers are used to finish knitted garments. They can be used for both synthetic fiber garments and their blends. This finishing process involves no pressure system and reduced handling of garments in the steam tunnel. At first, the garments are put on hangers and fed through a cabinet using a motorized rail. Steam helps relax the fibers in the garment, and the tunnel avoids any other pressing processes after or before this operation. In different cases, it replaces the other pressing approaches. These tunnels consist of special infrared drying in some cases. The turbulence of blown air gives additional energy for removing creases from woven materials.
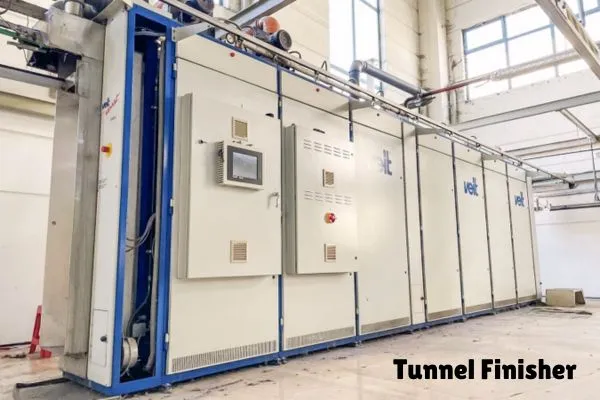
Press Cladding:
Bucks of steam presses and ironing tables for hand irons are typically covered with silicone foam, with the exterior side covered by a top cover of polyester-woven fabric. The heads of steam presses could be coated with various layers of materials, such as a layer of metal gauze for uniform steam distribution, a layer of synthetic felt to protect the next layer, a main layer of cotton knitted padding, and a final layer of outer cover, as on the buck.
Creasing machines:
This small press performs an exceptionally useful function in garment finishing. This pressing machine folds over and presses the edges of clothing components such as pockets or cuffs, following the easy sewing operation.
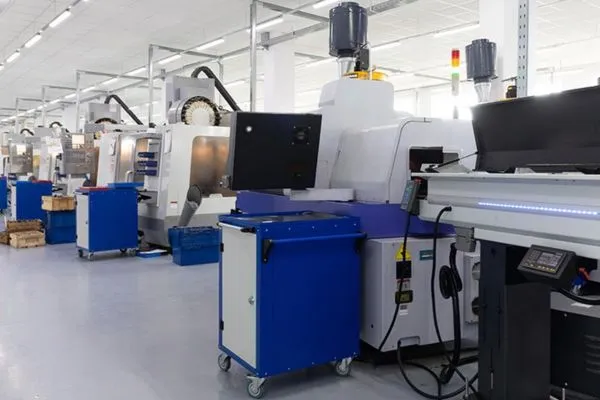
Pleating:
Pleating creates pleats, a type of fold formed during stitching by doubling fabric upon itself in the garment. However, these pleats can also be achieved through pressing by producing a series of wrinkles in the garment and pressing them into place. The pleats can also have different geometrical patterns. Pleating needs pressure, moisture, and heat. There are two types of machine pleating used in the production. One is a blade machine, where blades perform the main action, and the other is a rotary machine, in which the rollers are used.
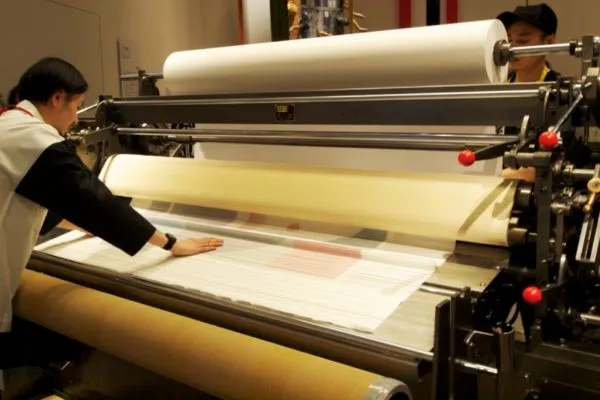
Block or die pressing:
Die pressing involves keeping the fabric over a fixed die before applying steam, heat, and pressure. Normally used for shaping hats and gloves during the manufacturing process. Another variety of automated die-pressing machines is applied for the combined folding and creasing of patch pockets as well as pocket flaps for clothes.
Permanent Press:
The permanent press decreases the strength of the fabric. This method was first introduced to produce better crease-recovering cellulosic fabrics. The technique consists of coating the fabrics during their production with a resin. After the resin treatment, a permanent press fabric is produced, which is then made into garments. The method is used for trousers to insert the required creases at the seams and hems and down the front and back.
Importance of Pressing the Garment
During the pressing garment process, unwanted wrinkles and desired creases and wrinkles can be intentionally added to enhance the finished look. However, this process has several other benefits too. By performing this finishing operation, a sewist can easily manipulate the shape of a garment to better fit the body or hide imperfections on the garment, such as puckered seams. Final pressing can have an aesthetically pleasing effect on garments and also create an overall glossy shine, boosting the item’s visual value.
There are many solid reasons to iron throughout your project, but we’re going to focus specifically on pressing this time. For a brief review, pressing means applying pressure to the material and raising it instead of gliding it over the cloth. This will result in a single, clean crease since it’s not about moving the iron around.
When pressing, one can get that polished look with seams that lay flat, like ready-made store clothing. It also gives an accurate cut when seams and creases are carefully pressed. Pressing seams is so important before sewing another seam that is going to cross it. Lastly, pressing has the special ability to create killer darts and a beautiful “memory” in fabric. Even after washing it or adding material, the fabric can retain its shape because of pressing. It creates the magic of a finished garment.
Conclusion
Pressing plays a crucial role in the production of finished apparel. Nowadays, with highly stylish garments evolving on a daily basis, the majority of which require a good feel and touch, it is always preferable to finish them with a form finisher, which helps to improve the garment’s finish. Pressing garments not only enhances the visual appearance of garments but also gives a professional finish and durability. Furthermore, cutting-edge pressing equipment and processes not only ensure outstanding garment quality but also showcase the dynamic combination of craftsmanship and innovation in the constantly shifting landscape of textile manufacturing.