Synthetic fiber spinning is a process in which an extruded liquid polymer filament is continuously drawn and solidified to form a continuous filament of synthetic fiber.
Table of Contents
There are 3 fundamental processes for the manufacture of synthetic fibers:
- Melt spinning,
- Wet spinning,
- Dry spinning.
Polymerization of fibers from polymer involves 3 steps:
1. Dissolution of polymer in the suitable solubilizing agent.
2. Extrusion of liquid solution through spinneret under pressure.
3. Continuous solidification of extruded liquid.
Polymerization Process
Chain Polymerization (Addition Polymerization):
Chain polymerization is a rapid self-addition of the monomer molecules to each other through a chain reaction. No byproduct is formed during this process.
Melt Spinning
Material: Thermoplastic polymers are used in the melt-spinning process.
➢ Melting: The polymer is a form of chips that is melted to a molten state.
➢ Extrusion: The molten polymer is pushed through a shower-like nozzle called a spinneret to create multiple filaments.
➢ Solidification: The filaments are cooled down and solidified using a quenching bath or by exposing them to air or a cold gas stream.
➢ Spooling: Once the filaments are solidified, they are wound onto spools. Then, they send for further processing into yarns or fabrics.
➢ Some common thermoplastic materials used in melt spinning include Polyethylene Terephthalate (PET), Polypropylene (PP), Nylon (PA), and Polyester. Some additional points about melt spinning are:
➢ The spinneret is designed to create multiple filaments simultaneously to increase production efficiency.
➢ The cooling process is critical. It ensures that the filaments are solidified into a stable and usable form.
➢ Thermoplastic polymers are ideal for melt spinning. Because it can be melted and solidified multiple times without significant chemical changes.
➢ The melt-spinning process is widely used in the production of synthetic fibers for various applications, including textiles, filtration, and composites.
Polymer Feed Hopper: The polymer chips are fed into the hopper and stored until needed for the extrusion process.
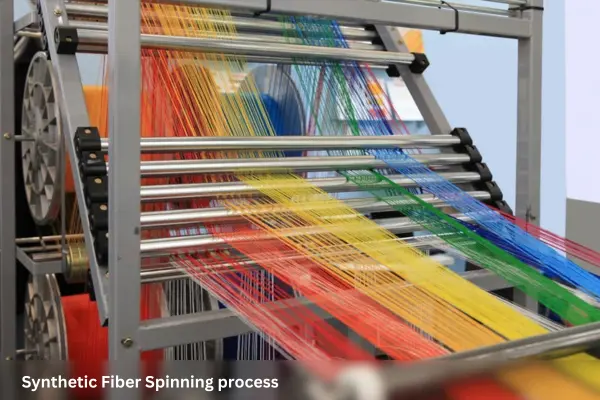
❑ Screw Extruder: At first, the polymer chips are melted. Then pushed forward by a rotating screw. The heat generated from the screw and the barrel of the extruder melts the polymer chips into a molten state.
❑ Metering Pump: The molten polymer is forced through a metering pump, which ensures that only the required amount is pushed forward.
❑ Filter Pack: The molten polymer is passed through a filter pack to remove solid impurities and gaseous bubbles and to homogenize the melt.
❑ Spinneret: The homogenized molten polymer is then extruded through a shower-like nozzle called a spinneret. The spinneret has many tiny holes. Through these holes, molten polymer is forced out, forming multiple filaments at once.
❑ Cooling and Solidification: Once the filaments are extruded from the spinneret, they are cooled and solidified using a quenching bath or by exposure to air or a cold gas stream. The solidified filaments can then be wound onto spools or processed into yarns or fabrics.
Melt spinning is mainly used to produce synthetic fibers from thermoplastic polymers. The process is easily scaled up to produce large volumes of fibers, making it a cost-effective method for manufacturing synthetic fiber.
Solution Spinning
There is another group of polymers called Thermoset polymers. On heating, this kind of polymer undergoes irreversible and permanent changes. For this reason, this polymer can’t be melted. Either it is degrading upon melting, or the melted condition is thermally unstable. So obviously, we can’t go for melt spinning and need a different system for them. So, the solution here is Solution Spinning. The polymer is dissolved in an appropriate solution and then spun in filament. After the filament is extruded, the solvent is removed. The solution spinning is again divided into two types depending on the solvent removal process.
- Dry Spinning
- Wet Spinning
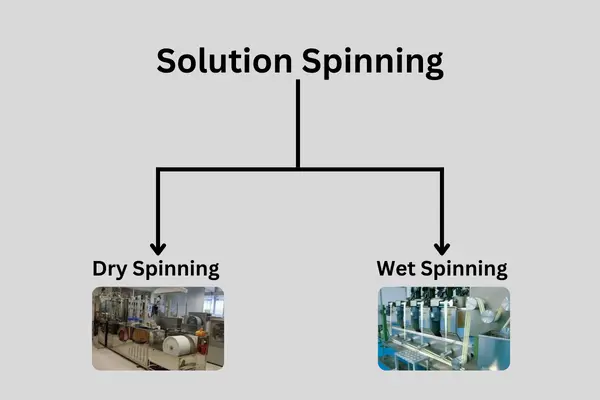
1. Dry Spinning:
In dry spinning, the filament is solidified, and the solvent is removed by evaporation with heat. Polymers (Cellulose acetate, Triacetate, Acrylic, etc.) are generated by the dry spinning process.
2. Wet Spinning
In wet spinning, the polymer solution is coagulated in another wet or fluid bath. This fluid dissolves the solvent, not the polymer. The polymer precipitates and filaments are obtained. Viscose Rayon, Lyocell, and Aramid are some examples of filaments produced by wet spinning.