Warping
Woven fabric is made out of two sets of yarn: warp and weft. Weft yarns run across the width of the fabric, while warp yarns run along its length. Warping is the initial preparation of yarn to weave fabric. The parallel winding of warp ends from onto a common package (warp beam) is termed warping.

It is the moving of several yarns from a creel of individual packages to a beam. A parallel sheet of yarn is wound onto the beam. The main purpose of warping is to create a package in which yarn ends remain consistently placed parallel and continuous, thus accelerating the next process, such as sizing or drawing in. Warping ensures that the set of yarns required to make a woven fabric is evenly tensioned and spaced before they are woven, providing the structural foundation for the fabric.
Table of Contents
Objectives of Warping
- To wind yarns parallel on a beam.
- Prepare a sheet with the required number of ends and the required pattern.
- To get the required effect on fabric and be a part of woven fabric.
- To increase the weave-ability of yarn.
- To begin the next process.
- To increase fabric production.
- Construction of warp yarn beams.
- Modifying yarn flaws such as thick and thin spots, huge knots, etc.
- Winding the specified length of yarn.
- Combination of small packages.
- To find the long length of warp yarn.
- To make a convenient yarn sheet for the sizing process.
- To wind up a predetermined length.
Requirements of Warping:
- Uniformity: The yarns should be evenly spaced under consistent tension all over the sheet, resulting in a smooth and even woven fabric.
- Length: To ensure the correct dimensions of fabric yarns, they need to be the same predetermined length.
- Number of threads: The sheet needs to contain the specific number of threads required for the weaving pattern.
- Condition: To prevent defects in the fabric, the threads should be error-free and unbroken.
- Quality Yarns: Yarns should have thickness and strength to avoid weak spots that could break during weaving.
- Cleanliness: Yarns must have no impurities in them.
- Measurement: To make sure the yarn lengths are equal, precise measurement is necessary. Accurate spacing of yarns is needed to match design and fabric specifications.
- Tension Control: Ensuring uniform tension across all warp threads to prevent weaving issues is required, as is equipment to maintain the tension throughout the warping process.
- Sizing Application: A sizing agent is applied to strengthen the yarns and reduce yarn breakages.
- Equipment: Creel is used to hold yarn packages and feed yarns smoothly to the warping machine. Warping machines help wind yarns onto the warping drum or beam.
- Warp Beam: For winding the prepared warp threads.
Quality of Good Warp:
- Enough and consistent strength
- Similar across the cross-section
- aligned warp tension
- uniform in size
- Less hairy and unclean
- The bare minimum of knots
- suitable or standard knot sizes and variations
- Absent of loose fiber and neps slubs
- Parallel arrangement of warp yarn in the weaver’s Beam.
The Warping Process Includes:
- Cone resulting from winding
- Creeling
- Controlling Mechanism
- Reed
- Measuring Instrument
- winding a beam

Types of Warping
Warping in textiles can be broadly categorized into two types and is popular in the textile industry for preparing warp yarn for power-driven high-speed looms or hand looms. Each type of warping method is suited for different types of fabric production and has its own set of advantages and requirements. These are:
- Pattern Warping or Sectional Warping.
- Beam-warping, direct-warping, or high-speed warping.
But there are different types of warping. Such as,
- Creel warping.
- Ball warping.
- Peg warping.
- Horizontal drum warping.
- Vertical drum warping.
Direct Warping or High-Speed Warping:
Direct warping is the process of drawing yarns directly onto the beam from individual packages on the creel. It is also known as high-speed warping or beam warping. This warping method is used to make smaller beams, which are combined later to produce the weaver’s beam. Direct warping is applied to manufacture grey towels that are dyed or fully bleached throughout the time of wet processing.
Nowadays, creels with moveable trolleys can be seen in modern beam-warping machines. Cones can be stored in reserve when one set of cones is operating in the machine because of the movable trolleys. Because of the difficulties involved in combining the ends, it is common practice to produce warper beams, which can contain up to 1,000 ends.

Patterned warper beams are not frequently made on the direct system, and any pattern that is produced is achieved by combining beams of various colors at the later stage of slashing. This imposes limitations that can only be overcome by moving to pattern weaving. A weaver’s beam can have up to 10,000 ends, and if this were to be produced straight away, it would be necessary to have up to 10,000 packages. A very difficult arrangement to accommodate and manage.
Process:
- Creeling: Multiple yarn packages are held on a creel.
- Winding: After creeling, winding action takes place. Yarns are wound directly onto the warp beam from the creel, ensuring that they are parallel and uniformly spaced.
- Beaming: Beaming is the final process of direct warping. The warp yarns are uniformly distributed and tensioned on the warp beam.
Advantages:
- The process is straightforward to set up because of its simplicity.
- Faster for smaller runs and simpler patterns. Operates at high speed.
- Compared to sectional warping, this process has lower setup costs.
Disadvantages:
- Not suitable for any complex patterns or fabrics requiring even yarn arrangements.
- Achieving uniform tension can be a bit challenging in beam warping.
Sectional Warping:
Sectional warping is the method of winding yarn onto a beam in sections, beginning at the tapered end of the beam. Sectional warping is mainly used for the weaving of towels containing stripes. Yarn with multiple colors can be contained in the weaver’s beam by using sectional warping. A slight angle in the drum of the beam prevents the yarns from slipping off.

This method is more versatile, making it ideal for producing larger quantities of fabrics with complex patterns. Segments of sectional warping are made sequentially, and because of this, the process is slow. Sectional warping is therefore mostly employed for intricate or short-run color combinations.
Process:
- Section Winding: Yarns are wound up onto a warping drum, which has a small length and controlled sections, ensuring uniform tension and spacing.
- Combining Sections: After that, each section is moved onto the warp beam one at a time until the full warp width is obtained.
- Beaming: On the warp beam, the sections are connected and uniformly tensioned.
Advantages:
- Suitable for complex patterns, and yarn arrangement is very even in this process.
- In the sectional warping process, it’s a lot easier to maintain uniform tension across the warp.
- Better large-scale production.
Disadvantages:
- More complex setup and process compared to direct warping, which is quite difficult to maintain.
- Higher initial setup costs are due to the need for more advanced equipment.
Warping Process of Yarn
However, the warping procedure for the terry towel is not as similar to the warping procedure for traditional weaving. The warping procedure is described below:
- The initial step in warping is creeling. Firstly, feed the empty cones in the creel. V-Creel is mostly used in industry among the other creels.
- At that point, the ends of the yarn go through the dents in the reed’s comb, which is known as denting.
- After the denting action, the yarns from the cones are wrapped onto an empty beam.
- Since a predetermined amount of yarn is warped in beam wraps, a separate yarn is inserted that helps to separate each yarn from each other during sizing action.
- Finally, the full beam is removed from the machine.
Warping Process Flow
The process flow of warping is given bellow:
Flow Chart For Warping:
Creeling
↓
Denting
↓
Empty Beam Feeding
↓
Sizing
↓
Drying
↓
Warping
↓
Leasing
↓
Ends Cutting
↓
Doffing
Sizing of Warp Yarn
The main purpose of sizing is to form a uniform layer of protective coating over warp yarn and lay down protruding fibers off of its surface. Sizing is the most crucial segment of the weaving preparatory process. The warping process initially depends on many factors, which include the material characteristics, the sizing ingredients, and the sizing operation.

In fabric manufacturing, the warp yarn is continuously subjected to substantial abrasive forces during the weaving process. As a result, the warp yarn needs to be stabilized by a polymer coating, or “size.”. A high rate of yarn breakage will result in a lower-quality product, but it also leads to a significant drop in the loom’s productivity.
Methods for Sizing Warp Yarn:
A sizing machine’s objective is to size the warp in a way that is optimal for the particular fiber type being used and for the final fabric construction, allowing the weaving process to be carried out smoothly and efficiently.
Sizing machines can be classified into three types according to the method of drying, as follows:
Conventional Sizing
Techniques of warp yarn sizing can be classified according to the method of application into conventional wet sizing, solvent sizing, cold sizing, and hot melt sizing.
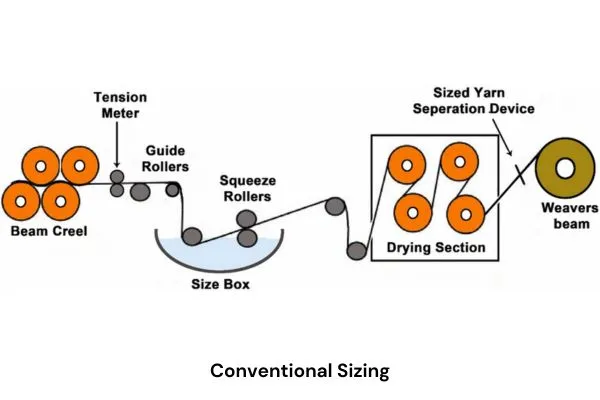
- Wet Sizing: In conventional wet sizing, the fundamental elements of the size recipe are the size materials and a solvent, usually water. Adhesives, softeners, and auxiliaries are classified as the main sizing materials.
- Hot melt sizing: suitable for high-speed weaving where there is a risk of yarn hairiness. This sizing is done in the warping machine by having a size applicator. Where the warp is kept pressed, the size is maintained in a cake shape.
- Foam Sizing: Here, water replaces the solvent. Sizeable foam is being used, and it needs to have mechanical, thermal, and liquid energy. Thus, production improves while 70% less energy is used.
- Blend Sizing: Manmade fibers are more sensitive to heat and tension, and because of that, blended sizing is being used for that. Furthermore, a successful size will work better than 100% cotton.
Non-Conventional Aqueous Sizing
- Double Cylinder Sizing: Double cylinder machine consists of two drying cylinders or two sow box arrangements which leads to more energy consumption
- Multi-Cylinder Sizing: In this sizing machine more than one sow box and several groups of drying cylinders are used. Densely spaced yarns are treated by it. Separate drying arrangements are used for warp yarns.
- Draw-sizing: This is a machine that links draw warping and sizing in a continuous process. A draw sizing system consists of elements like a creel, eyelet board, warp draw machine, intermingler, tension compensator, break monitor, sizing bath, dryers, waxing, and winding units.
Non-Conventional Dry Sizing
Although “dry” sizing has been around for a while, its industrial application has not fully taken off since the materials are so expensive. This is applied by spraying powder on the warp sheet. The size of the powder is fixed in the warp yarn to create an electrostatic force of attraction. In this process, the cost of raw materials and pollution is reduced.
What Warping Should Do?
1. To form a specified number of single-end packages, a continuous sheet of yarn of specified length & width is ensured.
2. Throughout the entire length of the beam, the individual yarn ends of the sheet should be equally distributed.
3. The yarn ends of the sheet should be wound at uniform tension in warping.
4. The density of the wound yarn beam should be kept uniform across the width & from start to end of winding the sheet to maintain a proper warping procedure
Warping Machine
These two are basic types of warping machines
- Sectional Warping machine.
- Beam Warping machine.
Elements of a Warping Machine
- Creel
- Guide Rollers
- Warping Drum
- Lease Rods
- Sizing Unit
- Drying Unit
- Warp Beam
- Tensioning tools
- Control System
Key Parameters of Warping Machines
Warping machines have several key parameters crucial for their operation and performance. Generally, warping speeds range from 500 to 1,500 rpm, with higher speeds increasing productivity but needing to maintain proper tension to avoid yarn breakage.
The warp beam capacity, which includes beam widths ranging from 1,800 mm to 3,600 mm and diameters from 800 mm to 1,200 mm, defines the maximum warp beam size compatible with processing. Modern warping machines can hold up to 1,000 to 10,000 ends. Creel capacity varies from 200 to over 1,000 positions and can be stationary, rotary, or mobile, which offers great flexibility in yarn selection and reduces interruptions.
Some textile machinery manufacturers are quite famous in the industry for manufacturing warping machines, such as Tsudakoma Corporation (Japan), Jakob Müller AG (Switzerland), Itema Group (Italy), Maschinenfabrik Textiltechnik (Germany), Stäubli Group (Switzerland), etc.
Warping process for denim fabric production
Ball Warping
Ball Warping is mainly used for Rope Denim production and direct warping is used for sheet Denim production. Ball warping prepares the log for the rope dyeing machine. Normally, magazine-type creels are used for the creeling of yarns in the form of cheese. This warping is an intermediate process for accumulating yarn for transport, dyeing, or reserving and it does not produce a beam. The number of ends taken is determined by the requirements of the following steps that will set up the weaver beam.

The length of rope on the log is generally 12830 meters. Leases are inserted at regular intervals that can be set automatically on the machine, generally every 100 meters. The lease also aids in yarn separation after sizing. Approximately 350 to 500 yarn ends are pulled from the creel in ball warping.
A comb-like device (reed) keeps each warp yarn separate and parallel to its close ends. A trumpet or condenser is a tool, where yarn sheets go through and become collapsed and condensed into rope form.

The two stages of ball warping begin with the warp yarns being wound into a rope and placed on a structure that looks like cheese. The ball is wound on a wooden core called a “log.”. In this process, warping is done in rope form onto balls, and a warp beam is prepared after the process. This type of warping process is suitable for denim fabric manufacturing, which involves a rope dyeing process.