Wool is hair fiber derived from the fleece of sheep, goats, and other animals. It has been a staple in human civilization for centuries. Its remarkable properties make it a sought-after material in various industries, from fashion to insulation. In this article, we will deeply discuss wool fiber.
Table of Contents
What is Wool Fiber?
Wool is a natural highly crimped protein hair fiber formed from sheep. It was the oldest fiber.
Wool-producing countries: (Origin of wool) Australia, New Zealand, India, China, USA, Argentina, Sudan, Iran, United Kingdom, and Turkey.
Source of Wool: (From which animals we can get wool). Merino ram, Angora goat, Angora rabbit, Vicuna, Alpaca, Camel, Guanaco, Cashmere goat, Mohair.
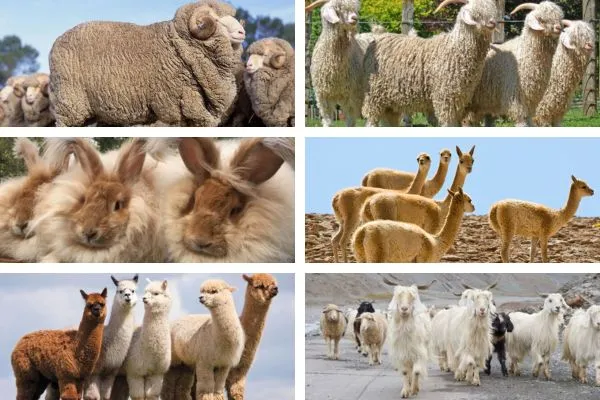
Classification of Wool:
Wool fibers can vary significantly depending on the breed of the sheep they are sourced from. Different breeds produce wool with distinct characteristics in terms of fiber diameter, length, and crimp. Merino, for example, is known for its fine and soft fibers, while breeds like Lincoln produce coarser wool suitable for carpets and outerwear.
You may like: Different Types of Wool Fiber
A) By Sheep:
- Class – 1: Known as Merino wool, Length is 1 – 5 “, mainly produced in Australia, New Zealand, South Africa
- Class – 2: Quality almost the same as class- 1, length is 2-8”, mainly produced in England, Ireland, and Scotland.
- Class – 3: Length is 4 – 8 “origin in the UK, used for garment making.
- Class – 4: Known as cross-breed wool, length is 1 – 16 “, used for carpet and blanket making.
The length of wool fibers also plays a crucial role in determining their suitability for various applications. Long-staple wool, with fibers over 2.5 inches in length, is preferred for spinning into yarns used in textiles. Short-staple wool, on the other hand, is often processed into felt or used in coarser fabrics.

Wool fibers are classified based on their diameter, often measured in microns. Fine wool, with diameters typically below 20 microns, is prized for its softness and is used in luxury garments. Medium and coarse wool, with diameters ranging from 20 to 40 microns and above 40 microns, respectively, find applications in carpets, upholstery, and industrial uses.
B) By Fleece
- Lamb’s wool: The wool which is the first fleece sheared from 6 – 8 months old sheep is called lamb’s wool. Its quality is very high.
- Hogget wool: The wool that is collected from 12 – 14-month-old sheep that have been previously shorn is called hogget wool.
- Weather wool: The wool that is collected from sheep older than 14 months after the first shearing is called weather wool. It contains soil and dust.
- Pulled wool: The wool which is pulled from the slaughtered sheep is called pulled wool.
- Dead wool: The wool which is collected from the dead sheep is called dead wool. Its quality is very low.
- Cotty wool: The wool that is collected from the sheep that are exposed to severe weather is called cotty wool.
- Tag locks: Torn, ragged, or discolored parts of a fleece are called tag locks. Its quality is very low.
C) By Fiber Extraction:
- Virgin wool: The wool that is collected from a lamb’s first shearing is called virgin wool. This is the smoothest and finest wool produced.
- Recovered wool: The wool that has already been made into yarns and fabric, and even yarn is called recovered wool. It is formed by the recycling process.
It has 3 types:
- Shoddy: Wool recovered from the fabric that has not been excessively milled or felted during manufacture.
- Mungo: wool recovered from cloths that have been milled or felted during manufacture.
- Extract: Wool recovered from cotton or rayon by carbonizing.
- All wool: The wool which contains a proportion of recovered wool is called all wool.
Types of wool Yarn:
Wool is cut into two types of yarn.
1. Woolen yarn: The yarn which is made from carded wool is called woolen yarn.
2. Worsted yarn: The yarn which is made from combed wool is called worsted yarn.
Learn about Difference between Carded yarn and Combed Yarn
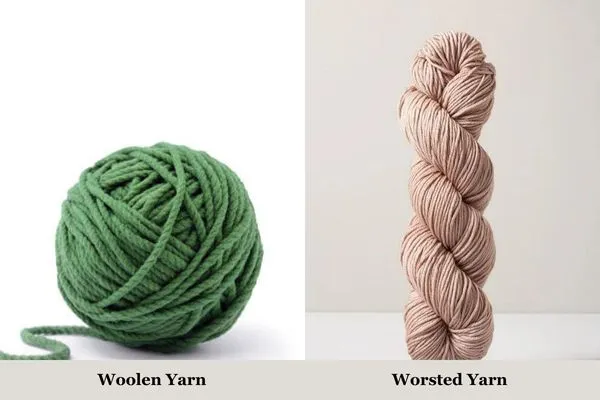
Difference Between Woolen and Worsted Yarn:
Woolen yarn | Worsted yarn |
i) Produced from carded wool. | i) Produced from combed wool. |
ii) Spun from short staple length fiber | ii) Spun from long staple-length fiber. |
iii) Slightly twisted | iii) Highly twisted |
iv) Coarser yarn | iv) Finer yarn |
v) Soften | v) Harder |
vi) Weaker | vi) Stronger |
Manufacture/ Production / Collection process of wool:
Shearing
⬇️
Sorting/ Grading
⬇️
Cleaning and Scouring
⬇️
Oiling
⬇️
Carbonizing
⬇️
Drying
⬇️
Bailing
- Shearing: Shearing is the process of cutting the woolen fleece of a sheep. The person who removes the sheep’s wool is called a shearer. Each adult sheep is trimmed once each year. A ram or male sheep has up to 20 pounds of raw wool.
- Sorting / Grading: Wool is classified into sections of different quality fibers from different parts of the body. The best quality of wool is used for clothing and the lesser quality is used to make blankets.
- Cleaning and Scouring: Scouring is the process of removing impurities from grassy wool using water, detergent, and mild alkali.
- Oiling: After scouring, the fiber is treated with various oils to keep it from becoming brittle.
- Carbonizing: Carbonizing is the process of removing vegetable matter (materials) from protein fiber using dilute or aqueous H2SO4.
- Drying: Wool fiber is dried by passing it through continuous flow heated air dryers. About 12 – 16% of the moisture is left to enable handling.
- Bailing: Bailing is the process of compressing graded and sorted wool by mechanical means.
Garneting: Garneting is the picking process of unused or recycled wool fiber.
Properties of Wool Fiber
Technical Properties of Wool Fiber are as follows
- Strength and Durability: Wool fibers possess excellent tensile strength. It makes them durable and resistant to breaking or tearing. This strength, combined with the natural elasticity of wool. That allows it to withstand repeated stretching and bending without losing its shape.
- Elasticity and Resilience: One of the most remarkable properties of wool is its elasticity. Elasticity enables it to stretch up to 30% of its length without breaking and then return to its original shape. This resilience makes wool garments resistant to wrinkling and helps them maintain their appearance over time.
- Moisture Absorption: Wool fibers have a high moisture absorption capacity. It can absorb up to 30% of its weight in moisture without feeling dampness. This inherent moisture-wicking ability keeps the wearer dry and comfortable in various climates. Which makes wool a perfect choice for activewear and outdoor apparel.
Flame Resistance
Unlike synthetic fibers, wool is naturally flame-resistant due to its protein structure. When exposed to flames, wool fibers char rather than melt or ignite, making it a safer option for clothing and furnishings.
Felting Property of Wool:
The felting of wool is the irreversible shrinkage of the length, breadth, and thickness of the material.
Wool felts because of the serrated surface of its fibres which is created by the overlapping epithelial cells or scales. Because of this serrated structure, less friction will result if the fiber moves in a root ward direction.
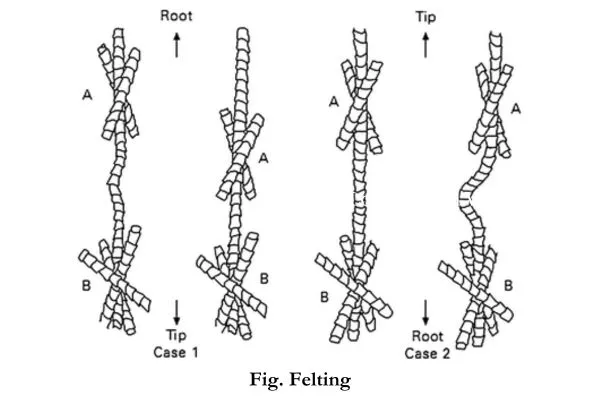
The difference in surface fraction is called directional fraction effect (DFE)
- Root
- Tip end
Physical Properties of Wool:
- Length: 60 – 100 mm, sometimes it goes 250 mm
- Diameter: 20 – 40 m
- Crimp: 30 crimp/inch
- Strength: 1.0 – 1.7 gm/ den
- Elongation: 25 – 35 %
- Specific gravity: 1.32
- Density: 1.31 gm / cm3
- Cross section: round or oval.
- Outer surface: serrated or scaly.
- Color: White to light cream.
- Hand feel: Soft
- Resiliency: Excellent.
- Abrasion resistance: Good
- Dimensional stability: bad
- Amorphousness: 70 – 75%
Chemical Properties of Wool:
- Effect of Alkalis: Wool dissolves readily in alkaline solutions such as 5% solution of NaOH
- Effect of Acid: Wool is more resistant to acid than alkalis. Although the polymer system of wool is weakened in the acidic solution, the fiber doesn’t dissolve.
- Effect of Bleaches: Wool containing chlorine compounds damages wool fiber.
- Effect of sunlight: Wool will weaken when brightened to sunlight for long periods.
- Colorfastness: Wool fiber is very easy to dye. Acid dye, basic dye, etc are used to dye wool fiber.
Thermal Properties of Wool:
Wool is renowned for its warmness, softness, and comfort. These make a preferred choice for garments worn close to the skin in winter. The natural crimp of wool creates an air bubble in the fabric structure, which helps to trap the air. Therefore natural crimp provides excellent insulation. It keeps the wearer warm in cold climates and cool in warmer temperatures.
Moreover, wool can wick moisture away from the body. It ensures dryness and comfort even during intense physical activity.
- Poor heat conductivity.
- Low heat resistance.
- Polymer fragmentation and surface discoloration.
- Scorching.
Chemical Composition of Wool:
- Keratin:33%
- Wax/ suint: 28%
- Fat: 12 %
- Mineral materials: 1 %
- Different impurities: 26%
Chemical Composition of Keratin/ Basic Elements of Wool:
- Carbon: 50 %
- Hydrogen: 12 %
- Oxygen: 10 %
- Nitrogen: 25%
- Sulfur: 3 %
Chemical Structure of Wool:
Why Ortho – cortex absorb more dye than Para cortex?
Para cortex contains higher cysteine than Ortho- cortex. Cysteine is capable of forming di-sulfide cross-links. So, the Para cortex cannot absorb more dye than the Ortho- cortex.
Which is more flexible between Ortho and Para cortex?
The ortho cortex is more flexible than the Para cortex.
How does wool keep us warm?
Due to the natural crimp of the wool fiber, each fiber is standing away from its neighbors. Air is trapped in the spaces between the fibers and creates an insulated layer that restricts the passage of heat through the fabric. That’s how wool keeps us warm.
Why does wool fiber have more amorphousness?
Ortho and Para more cortexes tend to spiral around one another. So the wool polymer chain cannot maintain order. For this reason, wool fiber has more amorphousness.
Structure of Wool Fiber
Topography/ Microscopic View of Wool Fiber:
Epidermis
Cortex
Medulla

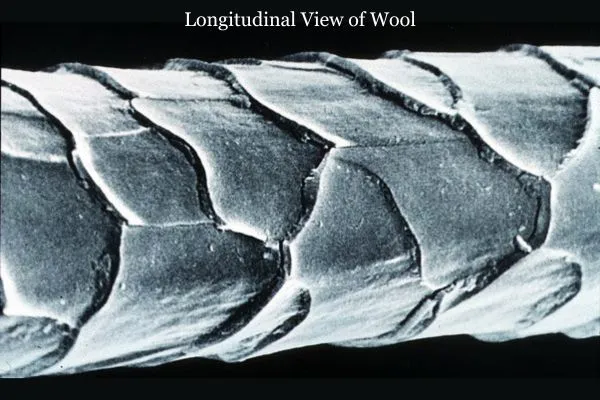
Morphological Structure of Wool:
Ortho cortex
Para cortex
Cortical cell
Wool polymer keratin
Proto fibril
Micro fibril
Macro fibrils
Epicuticle
Exocuticle
Endocuticle
Epithelial cell

Microstructure of wool:
The microstructure consists of 3
Main components:
1. The cuticle, 2. Cortex/ core, 3. Fibril
Cuticle: The cuticle is the layer of overlapping epithelial cells surrounding the wool fiber.
There are 3 cuticles:
- Epicuticle: Outermost layer.
- Exocuticle: Overlapping epithelial cells, largely responsible for felting shrinkage
- Endocuticle: Intermediate, cementing layer bonding between epithelial cell and cortex.
Cortex: The cortex forms about 90% of the fiber volume. It consists of spindle-shaped cortical cells. It is made of 2 distinct sections.
i) Ortho- cortex, ii) Para cortex
The ortho and para cortex spiral around one another, along the length of the wool fiber.
Difference Between Ortho Cortex and Para Cortex:
Ortho Cortex | Para Cortex |
i) Lower density | i) Higher density |
ii) More absorbent | ii) less absorbent |
iii) More flexible | iii) less flexible |
Fibril:
The cortical cells of wool fiber consist of numerous number of macro fibrils, each about 100 – 200 mm in diameter. Each macro fibril consists of hundreds of microfibrils, each about 5 nm in diameter. Each microfibril consists of eleven proto-fibrils, each about 500 nm in length and 2 nm in diameter. Finally, each proto-fibril consists of three wool polymers.
Why wool is comfortable to wear?
Due to the helical configuration of the Ortho and Para cortex, wool fiber has smoothness, flexibility, elasticity, and durability. So we can say that wool fiber has higher resistance properties. That is why wool fiber is comfortable to wear.
Why wool fiber is easy to dye?
Wool fiber has more amorphous regions than crystalline regions. So, dye molecules can easily enter the amorphous region of the fiber. Moreover, wool is more absorbent in nature.
For the above reason, wool fiber is easy to dye.
Alpha and Beta Configuration of Wool Polymer:
Alpha keratin: The helical configuration of wool polymer in its normal relaxed state is called alpha keratin.
Beta keratin: The unfolded configuration of the wool polymer after stretching is called beta keratin.
* Describe wool polymer.
i) A wool polymer is 140 nm long and about 1 mm thick
ii) A wool polymer is about 70-75% amorphous and 25 – 30 % crystalline.
iii) In its normal relaxed state, the wool polymer has alpha keratin. Structure and after stretching the wool polymer tends to beta keratin structure.
iv) Wool polymer is complex due to the presence of several important chemical groups and intermolecular forces of attraction.
Why structure of the wool polymer is complex?
The wool polymer is complex due to the presence of several important chemical groups and inters polymer forces of attraction.
Different Chemical Groups in Wool Fiber:
- Polar peptide group
- Carbonyl group
- Carboxylate group
- Amino group
- Cysteine
Different Bonding Present in Wool Fiber:
- Peptide bond
- H- bond
- Ionic bond
- Di-sulfide bond
- Van der Waal’s force
Identification of wool fiber:
- Physical test: the flame is steady but more difficult to keep burning. The smell of burning wool is like the burning of hair.
- Chemical test: wool fiber dissolves in concentrated sodium hydro-oxide and sodium hypo-chloride and slowly dissolves in 70% Nitric acid.
Application of Wool Fiber:
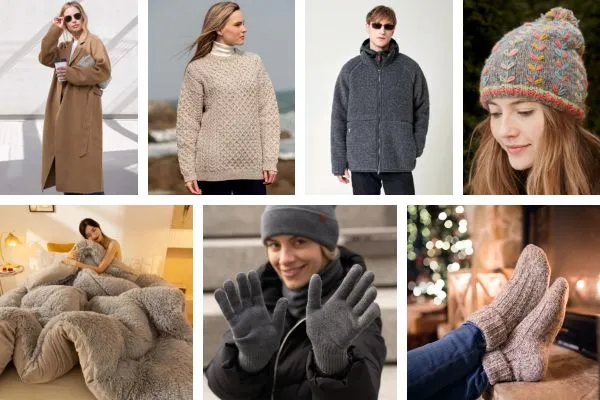
Wool fiber finds a wide range of applications across different industries due to its versatile nature and desirable properties. such as:
- Overcoats
- Sweaters
- Jackets
- Blankets
- Hats
- Gloves
- Carpets
- Socks
Substitute of wool fiber:
Acrylic fiber is a substitute for wool fiber. Because acrylic is a synthetic fiber that has similar properties to wool, easily available and its quantity can be increased or decreased as per demand. Hence, acrylic is positioned as a cheap substitute for wool.
Conclusion
Wool fiber stands out as a natural, and versatile material with a wide range of applications across textile industries. From its classification based on sheep breed, fiber diameter, and length to its technical properties such as strength, elasticity, and flame resistance, wool continues to be valued for its unique characteristics and sustainable attributes.