Textile winding can be defined as the transfer of yarn from a ring, bobbin, hank, etc. into a suitable package.
Table of Contents
What is Winding in Textiles?
Winding is the process of creating large yarn packets that are simple to unwind. This makes using subsequent machines easier and more cost-effective. Winding can be both electrical and mechanical. In simple terms, winding means transferring yarn or thread from one type of package to another type of package.
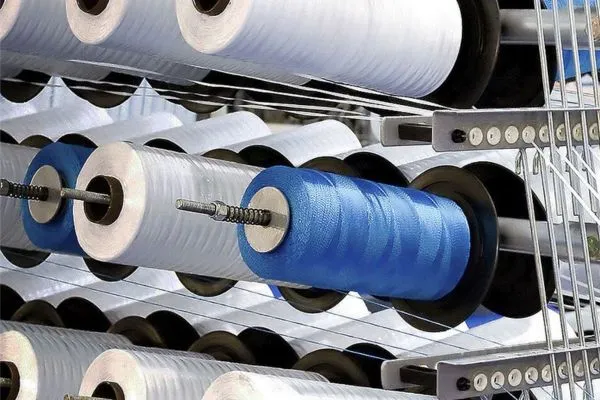
In fabric manufacturing, rewinding is more important than direct winding. The rewinding process is also a crucial operation in the fabric manufacturing process. After warping, some packages contain only a few grams of yarn, making further processes such as warping, twisting, and quelling inefficient. This specific need prepares a more dense and uniform yarn package of large size from unsuitable packages that can unwind in the following operations without any interruptions: rewinding.
When the yarn package passes through a tensioned and controlled system, it becomes unwound, and a grooved cylinder helps to wound evenly around the package; the yarn enters the recess in the cylinder. As a result, the yarn’s translation corresponds to the cylinder’s rotation. Further functions of winding are to check the yarn and eliminate any defects found during the operation.
Objective of Winding
- Transferring yarn from one package to another can be conveniently used for the weaving process.
- Removing yarn faults like hairiness, naps, slabs, and foreign matters.
- Cleaning yarn.
- To improve the yarn’s quality
- To obtain an appropriate bundle
- To keep the yarn stored.
- To reduce the end breakage.
- Enhance productivity.
- Storing the yarn in a suitable package.
- Acquiring the necessary yarn package.
Requirements of Winding
For an effective yarn winding process, some requirements need to be fulfilled.
- The level of defects in the yarn must be reduced to an acceptable level.
- The yarn must not sustain any kind of damage during the winding process.
- The yarn must be wound in such a way that it can be unwound easily in the following process at the required speeds.
- For the particular end use, the package size, shape, hardness, and build must be the most technologically suitable.
- The package size should be controlled in the winding process to fulfill the particular economic requirements.
- The winding operation must be designed to provide the best economic performance possible across the whole fabric manufacturing process.
- It is important to maintain the yarn’s properties and to avoid knitting it too loosely or too tightly.
Types of Yarn Winding
The process of winding yarns from bobbins, rings, and hanks into simpler containers such as cops, cones, or pirns is recognized as winding. Yarn winding is an important step in the textile manufacturing process, where yarn is wound precisely onto a suitable package for further processing or storage. Yarns for the warp and weft are wound on separate components. Weft yarns are woven on the cops and pirns packages, whereas warp yarns are wound on cheese, cone, and flanged bobbin packages.
There are many processes and types of yarn winding, depending on the yarn’s intended usage and specifications. The following are some frequent types of yarn winding:
- Precision Winding: Mainly high-quality and fine-count yarns are wound by precision winding. It keeps winding the yarn onto a package with precision tension control to enable uniform and smooth winding. Precision winding is necessary for yarns used in knitting and weaving.

- Random Winding: This winding technique is typically used for coarser yarns and bulkier fibers. In a random winding method, yarn is wound onto a package without strict tension control, resulting in a more uneven and sophisticated winding pattern. It is often applied to create textured or slub yarns.

- Coning: the process of winding yarn onto a cone-shaped package is referred to as coning. Cones have been frequently used for dyeing, knitting, and weaving operations, as they give better unwinding control and can be easily mounted on various textile machines.

- Cylindrical Winding: Cylindrical winding is mainly designed to wound yarn onto a cylindrical package. Yarns with a higher level of tension control and precision are suitable for this winding. Weaving and warp knitting are both carried out using cylindrical packages.
- Cross-Wound Package /Cone or Cheese: Cross-wound packages, often known as cones or cheese, are wound diagonally to offer great stability and balance. Cone or cheese packages are commonly used in weaving, warp knitting, and crochet applications.
- Pirn Winding: Pirn winding is a specialized winding process used largely in the weaving industry. Pirn means weaver’s bobbin, spool, or reel. It usually involves winding the yarn onto a shuttle pin, which can be seen in shuttle looms for weft insertion.

- Precision Coning: Precision coning connects the features of precision winding and coning. Winding yarn onto a precision-controlled cone package, ensuring uniform winding and tension control, is mainly done by this process. High-quality warp knitting and weaving yarns work well with this technique.

- Parallel Winding: Parallel winding is the process of winding yarn onto parallel tubes or spools. Since it provides uniform tension and prevents yarn distortion, It is often used in filament yarn production.

- Doubled and Twisted Winding: This kind of winding incorporates winding onto a package while twisting two or more yarn strands together. Doubled winding is frequently used for producing plied yarns, which have improved strength and stability.

- Autoconing: Autoconing is the first automated winding process that includes three functions, precision control of tension, yarn clearing, and splicing. It can give high-quality, uniform packages and is also commonly used in large-scale textile manufacturing processes.

Types of Winding Packages in Textile
Basically, there are two kinds of winding, according to the winding way.
- Precision winding.
- Non-precision winding.
Precision Winding:
Precision winding is widely used in the manufacturing process to wind materials such as yarn, wire, or film onto a spool in an organized and controlled manner. In precision winding, successive coils of yarn are held close together in a parallel or near-parallel manner. This procedure allows for the production of a highly dense package with the maximum amount of yarn stored in a given volume. This creates a smooth, evenly wound package that’s easy to use after production. This method also ensures that the material is free of tangles, overlaps, or gaps. This winding method is crucial in various industries, including textiles and packaging, where consistent tension is the main focus for the quality and functionality of the final product.
Features of Precision winding:
- A reciprocating traverse wound package.
- Patterning and rubbing damage packages.
- The package carries more yarn.
- The package has less stability.
- The package is very rigid and compact
- The package is highly dense.
- The rate of package unwinding is low, and the process is difficult.
- The successive coils are arranged in a parallel or near-parallel manner
Five Key characteristics of precision winding are:
- Consistent Tension
- Accurate Layering
- High-Speed Winding
- Reduced Waste.
- Improved Quality
Non-precision Winding:
Non-precision winding is a less controlled process for winding materials like yarn, wire, or film onto a spool. This type of winding makes the package formed by a single thread, which is held by a package at an appreciable helix angle so that the layers cross one another and give stability to the package. The packages formed by this winding are less dense but more stable than the precision winding package.
Non-precision winding, as compared to precision winding, does not place a high value on intense control over material placement and tension, resulting in a more random or loosely structured winding pattern. This method is typically used in two cases: when the exact arrangement of the material is less critical following the final application and when the material will be rewound further in a way that corrects any irregularities.
Features of non-precision winding:
- Only a single coil is used to make this package
- The cross-winding technique is mostly applied.
- The package has very low density.
- The minimum number of yarns that can be wound.
- The formation of the package is soft and less compact.
- The stability is improved.
- No flanges are required in this winding.
- The unwinding rate is comparatively high and the process is easy.
Key characteristics of non-precision winding are:
- Variable Tension
- Random Layering
- Lower Cost
- Higher Waste Potential
- Suitable for Certain Applications
Package winding can be categorized as follows:
- Pirn Winding
- Pool and Cop winding
- Cone Winding
- Cheese winding
- Flanged winding
Faults encountered during winding:
- Yarn Breakage during winding
- Twist Variation
- Incorrectly formed winding
- Unclean packages
- Package of hairiness
- Poor unwinding.
- A winding bundle that is softer or harder at a high pace, etc.
Types of Winding Machines
Winding machines have various forms, each one designed to handle specific materials and applications. Some of the winding machines have been mentioned below:
Coil Winding Machine:
This type of winding machine creates coils, essential components in transformers, motors, and inductors. They can work with a variety of wire diameters and forms, creating coils that are cylindrical or toroidal (donut-shaped).
Film Winding Machine:
As the name suggests, film winding machines wind plastic films used in packaging, insulation, and other applications. They are capable of handling fragile plastic materials quickly.

Rope Winding Machine:
Ropes, cables, and other thick materials are wound by these machines onto spools or drums. Rope winding machines are often used in the construction, marine, and manufacturing industries.

Paper Winding Machine:
Paper winding machines work with large rolls of paper to wind them into smaller tubes. This is important for transforming paper mill rolls into shapes suitable for printing presses or industrial applications.

Textile Winding Machines:
There are various winding machines specific to textiles, such as bobbin winders, pirn winders, cone and cheese winders. They prepare yarn for weaving, knitting, and other textile applications. These machines can enhance yarn quality by troubleshooting defects and ensuring even winding.

Winding Process in the Textile Industry
The main goal of the winding process in textiles is to get yarn ready for knitting or weaving, the following steps in the production process. The usual steps are broken down in the following order:
Load the creel
↓
Unwind the yarn
↓
Tensioning and cleaning
↓
Winding onto a new package
↓
Doffing
Textile Winding Machine
Winding machines play a crucial role in the textile industry because they wind yarn, thread, and other fibers onto spools, bobbins, or cones. These machines make sure that the material is wound correctly for subsequent operations such as weaving, knitting, or stitching. The following are some common types of textile winding machines:
Cone-winding machines:
- Automatic Cone Winders: These machines automate the whole winding process. At the same time, it provides consistent tension and alignment.
- Manual Cone Winders: Operated manually. These cone winders are mostly suitable for smaller-scale operations.
Bobbin Winding Machines: Bobbin winding machines wind yarn onto bobbins, commonly used in sewing machines and many industrial weaving machines.
Precision Winding Machines: Ensure that the yarn is wound with accurate tension and alignment, which will reduce faults and improve the end product quality.
Drum Winding Machines: Drum winding machines are utilized for winding yarn onto large drums, typically for industrial applications where large volumes of yarn are processed.
Hank-to-Cone Winding Machines: This type of machine is designed to wind yarn from hanks onto cones, ensuring uniform tension and preventing tangles all over the package.
Soft Package Winding Machines: Soft package winding machines create loosely wound packages that are easier to dye and have an excellent dye penetration property throughout the yarn.
Hard Package Winding Machines: Develop tightly wound packages that are more compact and suitable for shipment and storage.
Rewinding Machines: Rewinding yarn from one package to another is a common method for removing defects or preparing yarn for a specific use.
Parallel Winding Machines: Wind yarn in a parallel manner, creating packages with yarn layers that lie parallel to each other. This is often used for specific textile applications where this winding pattern is beneficial.
Cross-Winding Machines: Cross-winding machines create a criss-cross pattern to prevent tangling and facilitate easy unwinding, commonly used for winding thread and fine yarns.
Cheese Winding Machines: Cheese packages have one kind of cylindrical shape that winds yarn into cylindrical packages, used primarily in the knitting industry.
Auxiliary Functions
A winding machine has the following auxiliary functions:
- Creeling: Creeling is the removal action of an empty package and moving to the full package in the feed region of the machine, ready to be unwound as part of the transfer process.
- Piecing: Finding the ends of the packages and connecting them is known as the piecing process.
- Doffing: Doffing action means removing the full package and placing the empty package in the delivery region of the machine, ready to receive yarn as part of the transfer process.
Driving Methods for a Winding Machine:
- Driving with surface contact
- Direct package driving at a steady speed
- Direct package driving at varying speeds
Factors of winding machine efficiency:
- Spindle or drum speed: Spindle speed is proportional to winding efficiency.
- Yarn Count: A higher yarn count means higher winding efficiency.
- Yarn quality: If quality improves, then winding efficiency also improves.
- Worker efficiency: The winding will be more efficient if the work is performed efficiently.
- Humidity: Humidity is reciprocal to winding efficiency.
- Workload per worker: Winding efficiency will get better when each worker has less labor to do.
- Power failure: Winding efficiency will drop as the power failure rate rises.
- Creating time: The efficiency decreases as the creeping time increases.
- Doffing time: An increase in doffing time results in less efficiency.
- Capacity utilization: Efficiency rises with a decrease in capacity utilization.
QUALITY CONTROL IN WINDING SECTION
- Shade matching: The dyed yarn was compared with a swatch card or lab drip sample.
- Level Checking: Chemicals used to dye packages are pushed into the container through the process. Thus, it may be feasible for the inner and outer sides to have different levels. After verification, let up to 5–6%
- Fastness: Color and water fastness are tested.
- Strength: CSP, tenacity, CV% of tenacity, and elongation are tested.
- Package hardness: The soft wound package is manually checked. It will not shade properly if it is hard. Inspections are also made on the hard-wound package.
Conclusion
Winding is one of the most important techniques used in the textile sector, and it is mainly used in the spinning section. However, it is also important in fabric manufacturing.