What is Desizing in Textile?
Desizing is the process employed to remove the sizing material from the fabric. It is the first wet-processing textile finishing proccess used to remove the sizing material from the fabric applied for specific production benefits.
The Desizing Process is done to remove size from the warp yarn of the woven fabric yarn is coated with a sizing agent period to reduce their functional properties and decrease breakage in the loom at improving productivity by increasing weft insertion speed.
The desizing process in textiles is the first wet preparatory process textile finishing technology employed to remove the sizing material from the fabric applied for specific benefits of production.
The desizing process in textile industry is a chemical process and the rate of this process i.e., the rate of hydrolysis of starch, can be controlled.
Desizing in Textile Depends on-
- The Solubility of the film-forming polymer (Size).
- The viscosity of the size in the solution.
- Amount of size applied.
- Nature and amount of the plasticizers.
- On the effects of numerous subsequent wet processing steps.
- On the interaction with added chemicals.
- Fabric Construction.
- Method and nature of washing off.
- The temperature of washing off.
Importance of Desizing in Textile Industry
Desizing is an essential part of the purification process for woven fabric. Size performs an adhesive and lubricating function. After drying, the size forms a protective film on the surface of the warp yarns, bounding the protruding fibrils to produce a smoother yarn with improved tensile strength and abrasion resistance.
The Application and Properties of Sizes:
The essential aim of sizing and desizing in textiles is to increase productivity in weaving. This is achieved through a reduction in yarn breakages that permits increased running speeds. Indeed, the high speeds of modern weaving processes could not have been realized without corresponding improvements in sizing technology. The most important requirements of a size formulation can be summarised as follows:
- High adhesion and good film-forming properties on the yarn, together with good elasticity of the applied film.
- Low tendency to foam in the application of liquor.
- Freedom from skin formation in the application of liquor.
- Good storage stability.
- Good compatibility of wash-off liquors containing different-size components
- Appropriate compatibility with alkalis and bleaching agents if de-sizing is not carried out separately from
scouring and bleaching.
Objects of Desizing:
The objective of sizing is to improve weaving efficiency by reducing the number of yarn breakages, reducing frictional wear of loom parts, and allowing increased running speeds.
- To remove starch from the fabric.
- To increase the absorbency of the fabric.
- To increase the luster of dyeing and printing.
- To make the fabric ready for the following subsequent process.
Different types of size materials:
Starch: | Corn, Potato, Sago, Hydroxyethyl starch. |
Natural gums: | Tragacanth, locust bean etc. |
Proteins: | Glue, Gelatin |
Synthetic sizing agent: | PVA, PVC, PAN, PAA. |
Additives: | Defoamers, Thinners, Tallow, Oils and waxes |
Types of Desizing in Textile Industry:
There are two types of Desizing is practiced in our textile industry. These are:
- Hydrolytic Desizing Method
- Oxidative Desizing Method

A. Hydrolytic Desizing Method:
- Rot Steeping.
- Alkali steeping.
- Acid steeping.
- Enzymatic Desizing.
a. Rot Steeping:
Starch is removed by rotting. Rot Desizing is the oldest method when a man cannot know the use of enzymes or other special chemicals.

- It is the very oldest method.
- No special chemicals are required.
- In this method, the fabric is passed through a padding mangle containing warm water of 40- 600C & then kept for a long stocking for 12-24 hours depending on warm water temp.
- Pectin & organisms naturally present in water produce liquefying starch enzymes that remove starch. But starch is not completely removed.
- To remove more starch, more time is required. However, for prolonged stocking, the enzymes may attack the cellulose. After washing, de-sizing is completed.
- Here, Temperature is mainly controlled.
- Oldest and Cheapest method.
Advantages:
- No chemical was used.
- Cheap process.
Disadvantages:
- Ample floor space is required.
- Prolonged process.
- Discontinuous process.
b. Alkali steeping:
In the Alkali steeping process, the starch is removed by alkaline hydrolysis. Fabric is treated with 0.4-0.6% NaOH solution at 60-70˚C & stored for 8-10 hours.
Precaution: Care must be taken that goods don’t dry up; it causes a partial concentration of alkali.
Advantages:
- Economically used and cheap.
- Mercerizing can be done in the same alkali (reusable).
Disadvantages:
- Considerable shrinkage may occur.
c. Acid Desizing:
In the acid desizing process, the starch is removed by steeping with acid. The fabric is treated with 0.5-1.0% dilute Sulphuric acid solution or HCl acid at 40-60˚C for 4-6 hrs to hydrolyze the starch from the sized fabric.
Advantages:
- The amount of size removed is comparatively more tremendous.
- Not possible to shrinkage.
Disadvantages:
- Large floor space required.
- Discontinuous process.
- In a risky process, hydrolytic degradation causes the strength of cotton.
d. Enzymatic steeping / Enzymatic Desizing:
The enzymatic Desizing method is a traditional process that is most commonly used nowadays. The following stages complete the whole process:
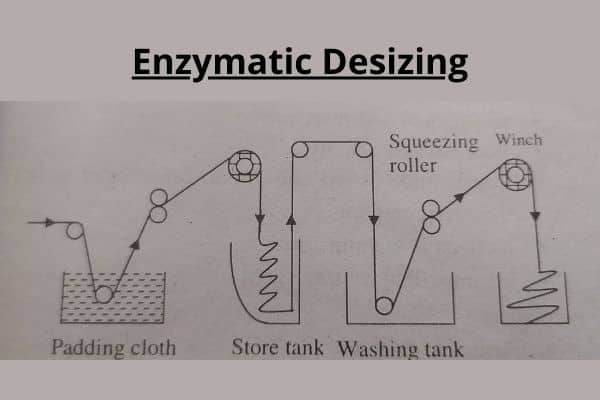
Preparation of Enzymatic Desizing Process:
i. Desizing Recipe:
- The enzyme (malt extract): 0.5–2%
- Chelating Agent/salt (if necessary)
- Temp: 50-60˚C
- Time: 3-4 hours
- pH: 6-7.5
ii. Padded in padding mangle: The sized fabric in rope form is immersed into the de-sizing liquor by immersion roller. The consumption rate should be regulated so that the mixer level remains constant.
iii. Storing: Then, the fabric is squeezed & stored for 3-4 hrs at room temperature. Here, enzymes react with starch & decompose into glucose.
iv. Washing: The fabric is washed, squeezed & dried.
What is Enzyme?
Enzymes are living organisms based on the protein which is used as Bio-catalyst. Its molecular weight is high.
The action of enzymes is controlled by temp, concentration, time, and pH of the solution. Its primary function is the fermentation of starch. Enzymes are soluble in water but insoluble in acid and alcohol.
Types of Enzymes:
Mainly two types
- Cellulose enzymes: They degrade cellulose & then convert it to glucose.
- Analysis enzymes: They only hydrolyze starch but don’t attack cellulose.
Types of analysis enzymes are:
i. Malt extract enzymes: Extraction of freshly germinated barleycorns. It performs best at 600C & destroyed at 750C.
Trade name: Disastafor, Ferment D, Terhyd MD etc.
ii. Bacterial extract enzymes: Obtained from rice grains & breaks down starch into water-soluble dextrins. It performs best at 70-750C & destroyed at 95-1000C.
Trade name: Rapidase, Biolase, Bactolase, Gelatase, Acry.
iii. Pancreatic analysis enzymes: Prepared from the pancreas of slaughtered animals. It can modify starch, albumen, pectins & fats. Trade name: Fermosol, Novofermosol DS, Degomma, Viveral.
Condition of Desizing of Different Enzymes:
Enzymes | Temp | PH | Required Concentration |
Malt Extract | 55 – 600C | 6 – 7.5 | 3 – 20 gm/L |
Bacterial | 60 – 700C | 5.5 – 7.5 | 0.5 – 1 gm/L |
Pancreatic | 50 – 550C | 6.5 – 75.5 | 1 – 5 gm/L |
Problems in Enzymatic Desizing and Remedy:
1. Incomplete desizing:
Causes-
- Inadequate enzyme
- Inappropriate de-sizing bath PH
- Inappropriate de-sizing bath temperature.
- Insufficient fabric pickup.
- Insufficient digestion time.
- Poor enzyme activity.
- Deactivation of the enzyme due to the presence of metals or
- their contaminants.
- Ineffective wetting agent
- Incompatible wetting agent
Remedies:
- Sufficient enzyme
- Optimum PH
- Optimum temperature.
- Optimum squeeze pressure and use of the wetting agent.
- Optimum digestion time.
- Use of good enzyme
- Use of soft softener and
- use of an appropriate
- sequestering agent.
- Use of good and effective wetting agent.
- Use of compatible wetting agent.
2. Uneven de-sizing (widthwise):
Causes-
- Uneven pad pressure (across the width)
- Non-uniform pad temperature
- Non-uniform chemical concentration to the bath.
Remedies-
- Uniform squeeze pressure
- Uniform bath temperature
- Uniform chemical concentration.
3. Uneven desizing (lengthwise):
Causes-
- Uneven pick up along the length
- Preferential drying of the outer layer of the bath.
- Temperature variation during digestion.
Remedies-
- Uniform pick-up along the fabric length
- Cover the batch with polyethylene or other suitable sheets.
- Keeping the batch rolling.
4. Uneven desizing (random)-
Causes-
- Poor wetting agent
- Inappropriate bath temperature
- Foaming in the bath
- Improper use o defoamer
- Uneven liquor distribution during padding
- Non-uniform washing after desizing.
Remedies-
- Use of effective and compatible wetting agent
- Optimum bath temperature
- Use of appropriate defoamers
- Uniform liquor distribution during padding
- Through and uniform washing after desizing
Problems in Textile Desizing:
1. Problems arising in pretreatment:
- Over drying the sized warp.
- The high content of fats with poor emulsion properties waxes subsequently applied to the warp
- The high content of finishing auxiliaries released from the synthetic component during sizing polyester/cotton (pc) products.
- Higher content of preservatives.
- The higher copper content for the size hydrolyzation plant and size trough.
2. Problems arising from the process itself:
Liquor uptake is too low because the impregnation box is too small or too little textile surfactant has been added.
The swelling time is too short.
Enzyme toxic surfactant has been used. The washing power is too small to remove the hydrolyzed size.
Controlling points of desizing:
- Pipelines.
- Faults bottom.
- Steam line.
- Multitubular heater.
- Inlet outlet pipe.
- Bulb.
- Temp.
- PH
B. Oxidative Desizing Method:
- Bromite de-sizing.
- Chlorite de-sizing.
- Ammonium persulfate de-sizing.
a. Chlorine Desizing:
- In oxidative desizing in textile, the starch is oxidized and this process is also known as grey chemicking.
Gaseous chlorine is used as an active reagent in this type of oxidative desizing. - The grey cloth is impregnated with water in a two-bowl padding mangle.
- The impregnated fabric is passed through a chamber provided with a false bottom, through which gaseous
chlorine is blown into the chamber at a constant concentration.
Chlorine reacts with the water present in the cloth, producing nascent oxygen and hydrogen chloride-
Cl2+H2 → 2HCl + [O]
- The nascent oxygen then attacks the starch thereby solubilizing.
- By controlling the quantity of chlorine and the time of contact between the cloth and chlorine, the oxidation of cellulose, which is more difficult to oxidize than starch can be prevented or minimized.
- The chlorine gas may be replaced by dilute hypochlorite solution, in which case it may contain 1.5-2.0gm/L of available chlorine using sodium hypochlorite or bleaching powder.
- The cloth may be impregnated with the solution at 30°C, squeezed, and allowed to stand for 1 hour at 3000C.
- It may be washed and sent for the next process of scouring.
b. Brormite Desizing:
- Sodium bromite, the salt of bromous acid, HBrO2 has powerful oxidizing action on starch.
- Sodium bromite attacks the starch of fabric and oxidizes by solubilizing of starch.
- It attacks reducing impurities quickly but does not affect cellulose.
The action of bromite de-sizing depends on:
- Concentration(1-2gm/L)
- PH(10-10.5)
- Temperature (Room temperature to 50°C).
- Time (30-45min)
c. Chlorite Desizing:
Sodium chlorite can be used under acidic conditions for oxidizing the starch present in grey cloth.
- In this method, the sized yarn is treated with a solution of sodium chlorite (3gm/L), buffered to PH
4(acidic mixture) at 80°C for 3 hours. - The yarn was washed, dried, conditioned, and weighed.
- The loss in weight indicated the extent of de-sizing.
96% of the total size was removed by the chlorite de-sizing method.
Desizing Identification Test: Tegewa Scale Desizing Test
After resizing, the Assessment of desizing efficiency tegewa scale desizing test needs to ensure the de-sizing
- Potassium Iodide (KI): 0.24 gm.
- Iodine (I2): 0.13 gm.
- water: to make 100 ml solution.
If one drop of this solution falls on the sizing MTL, then the following incident may occur.

- The deep blue → presence of starch.
- Violet → Partially degraded starch (dextrin).
- Brown→ Completely degraded to dextrin.
Comparison between Rot, Acid, Alkali and Enzymatic Steeping:
Topics | Rot Steeping | Alkali Steeping | Acid Steeping | Enzymatic Steeping |
Temp. | 40-600C | 60-700C | 40-600C | 50-600C |
Stocking | 12-24 hrs | 8-10 hrs | 4-6 hrs | 3-4 hrs |
De-sizing
Material | Water | Alkali | Acid | Enzyme |
Shrinkage | May occur | Occur | Don’t occur | Don’t occur |
Degradation Risk | prolonged stocking may degrade | Never | Concentrated acid may degrade | Cellulose enzyme may degrade |
PH | Neutral | High | Low | 6-7.5 |