What is Sizing?
Sizing is the technique of applying a protective layer onto the warp yarn surface so that the protruding fibers are wrapped onto the yarn surface / lapped to increase the weavility.
Table of Contents
Objects of Sizing:
1. To increase the weave ability
2. To increase the tensile strength of yarn
3. To increase smoothness of yarn
4. To reduce static electricity formation
5. To reduce the yarn breakage
6. To lap the protruding fibers on the yarn surface
Requirements of Sizing:
1. The sizing process must be efficient and economical.
2. The sized warp must be sufficiently strong, smooth, and elastic.
3. The tension of the warp yarns must be regular.
4. Yarn stretch and loss in elongation must be less.
5. The package must have a cylindrical shape.
Technical Changes Due to Sizing:
1. Breaking strength increases
2. Abrasion resistance increases
3. Stiffness increases
4. Flexibility increases
5. Hairiness decreases
6. Absorbency decreases
7. Electrostatic property decreases
8. Mass stress/ Linear density
9. Sized yarn
10. Unsized yarn
11. Strain
Sizing – weaving curve:
Warp breakage rate %
Weaving efficiency, n
Size add-on %
i) Initially the warp breakage rate decreases with the increase in size add-on %. This is due to the increase in yarn strength and reduction in yarn hairiness.
ii) The weaving efficiency, which is inversely proportional to the warp breakage rate, reaches its peak when the warp breakage rate is at its minimum.
Side View of Sizing Machine (Yarn path diagram of sizing process):
- Guide roller
- Top squeeze roller
- Immersion roller
- Size bath
- Bottom squeeze roller
- Drying roller
- Lease rod
- Creel unit
- Size box
- Drying unit
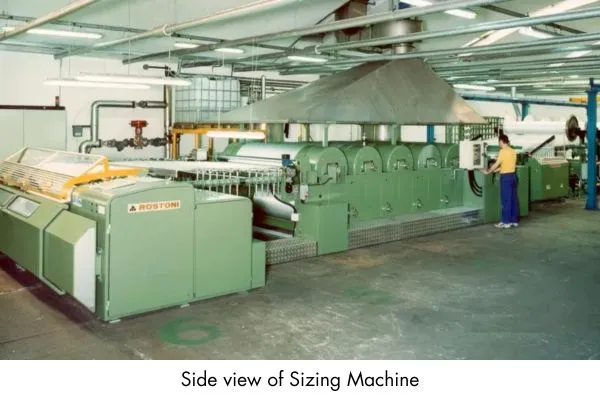
Units of Sizing Machine:
1. Creel unit
2. Size box
i) Guide roller
ii) Immersion roller
iii) Squeeze roller
3. Drying unit
4. Cooling unit
5. Leasing unit
6. Measuring unit
Size Cooking:
The process of mixing and cooking size materials at a certain temperature for a certain amount of time is called size cooking.
Size Box:
It allows the immersion of the yarns for a uniform and thorough penetration of the size & coating of the surface of the yarn.
Viscosity Cup/ Viscometer:
It is used to measure the viscosity of a recipe or liquid.
Example: Zahn cup.
Refractometer:
It is used to measure the amount of gritty particles.
Dip & Nip:
Double dip double nip
Size Ingredients/ Size chemical/size Recipe:
1. Adhesive: Starch, PVA, PVC, CMC
2. Lubricant: Animal fat, Mineral fat.
3. Anti-mildew agent: Zncl2, phenol
4. Anti-foaming agent: Benzene
5. Wetting agent: Mgcl2, Cacl2, Glycerin.
6. Weighting Agent: Sodium sulphate
Factors considered in choosing size ingredients:
1. It should give the fewest end
2. It should permit easy resizing
3. It should give good fabric characteristics
4. It should be compatible with machinery
5. It should not cause any health hazard
6. It should not cause a minimum
7. Its cost should be minimal
Function of Different Size Ingredients:
1. Adhesive: Increasing strength, smoothness, and abrasion resistance
2. Lubricant: Makes yarn soft and slippery
3. Anti-mildew agent: Prevents mildew formation
4. Anti-foaming agent: Prevents foam formation.
5. Wetting agent: Helps to wet yarn instantly
6. Weighting Agent: Increases weight of yarn
Controlling Parameters:
1. Speed
2. Viscosity
3. Squeeze of immersion roller
4. Height of drying cylinder
5. The temperature of the drying cylinder
Size Take–up %
The amount of size material added to the yarn surface is called size take-up %. It is determined by the following formula:
Size Take-up % = Weight of sized yarn – weight of unsized yarn/weight of unsized yarn × 100%
Factors affecting the size take-up %
1. Maturity: Maturity size take-up %
2. Hairiness: Hairiness size take-up %
3. Wet ability: Wet ability size take-up %
4. EPI: EPI size take-up %
5. Uniformity: Uniformity size take-up %
6. Warp tension: Wrap tension size take-up %
Sizing Techniques:
1. Hot melt sizing
2. Solvent sizing
3. High pressure sizing
4. Electrostatic sizing
5. Electrostatic sizing
6. Emulsion sizing
7. Combined sizing
Sizing faults & Their Causes:
1. Hard sizing: Due to applying too many size materials.
2. Shinery: Due to friction between yarn & drying cylinder.
3. Sandy warp: Due to not crushing the size/ grind material properly.
4. Ridge beam: Due to not optimum the viscosity of the size solution.
5. Uneven sizing: Due to the under or over-sizing process.
Drying Technique / Drying Method:
1. Cylinder drying
2. Hot air drying
3. Infrared drying
4. Combined drying
1. Cylinder Drying:
A) Two cylinder drying:
i) At first, the warp sheet is passed below the small cylinder & then over the bigger one.
ii) The yarn is dried while traveling through the circumstances of the cylinder.
B) Multi-cylinder drying:
i) A lot of cylinders are heated by passing steam.
ii) Heat gradually increases when moves towards the final cylinder and dries the yarn.
2. Hot air drying:
i) The warp yarn is placed in a closed chamber.
ii) Then hot air is blown into the chamber continuously to dry the yarn.
3. Infrared Drying:
i) The heating chamber consists of a plate that is consistently heated by a gas flame.
ii) The warp sheet is passed over the plate and dried in the process.
4. Combined Drying:
i) In this machine, pre-heating is done as a cylinder drying method.
ii) Final drying is done by the hot air drying method or infrared drying method.
Why sizing of filament yarn is necessary?
Multifilament yarns are continuous with no hairiness but contain some broken filaments. It may cause problems during weaving. That’s why sizing of filament yarn is necessary.