Interlining is a unique feature, a trim used in garment manufacturing as it helps to improve properties like appearance, shape, and durability of the garment.
Table of Contents
What is Interlining?
Interlining is a thick layer of mainly knitted, woven, or non-woven fabric placed between the fabrics of the garment. It prevents the outer fabric layer from wrinkling or unwanted stretching and also provides structural support to the garment. By hiding seam allowances, Interlining retains a clean and professional finish on garments.
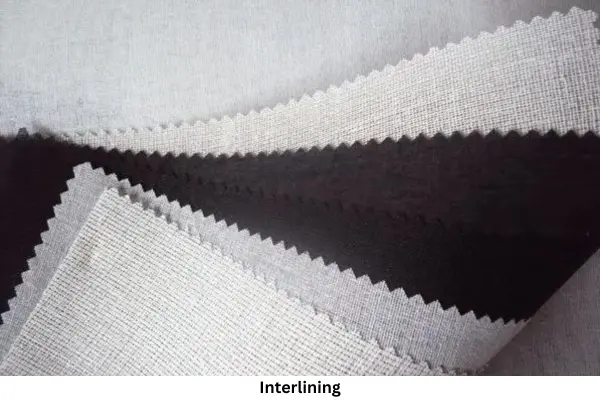
The interlining is also known as interfacing sometimes. Being an invisible part of a garment’s interior, its fusion process along with construction greatly influences the sewability, durability, and mechanical properties of the garment. Interlining is necessary for enabling shape into detailed areas such as the front of coats, collars, cuffs, and pocket flaps.
Working Principle of Interlining
Interlining is a unique feature, a trim used in garments. The working principle of interlining defines how it’s been processed and how it works for the apparel till the end use.
- After fusing to the outer shell fabric, interlining acts as a composite and stabilizes the outer shell against any distortion under any force.
- It enhances the aesthetic and hand feel of fused laminated material.
- Interlining also retains the shape of the fused fabric part during use and after-care treatment
- Interlining holds thickness and extra strength for a formal look to many garments.
- It works like an insulator, so it can be used as a thicker layer in any type of winter coat and jacket.
- Interlining can assess the sewing process of garments.
- Interlining materials are made of woven or non-woven fabrics, fusible or sewing suitable is needed based on the desired outcome and fabric compatibility.
Types of Interlining:
Interlinings are categorized by manufacturing methodology and finishes applied to the structure.
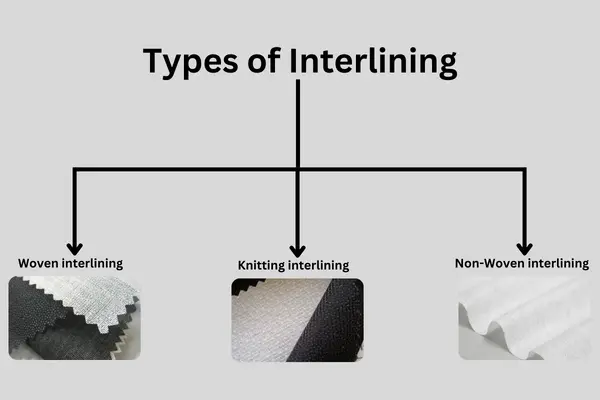
There are mainly three types of interlinings based on the structure of base fabric and technologies applied:
1. Woven interlining – Plain woven, twill woven.
2. Knitting interlining – Weft knitted or warp knitted
3. Non-Woven interlining – Needle punched, spun bonded, thermal bonded etc.
These interlinings are given specific coatings all over the surface like water repellent finish, wrinkle-free, anti-microbial finish to enhance the performance of garment functionality. Special finishes help the commercial wash processes in garments.
1. Woven interlining
Woven interlinings were used centuries ago mainly to strengthen or support coats, cloaks gowns, or hats. It was made from 100% cotton fabrics treated by starch application and was also non-fusible. However, due to some irregularities and unwanted hard touch during washing the garments have paved the way to the development of fusible interlinings. Usually, a layer of adhesive is applied on the normal cotton sheet fabrics to be fixed to the shell fabric. Heat or pressure is applied to do such a process. This alters the fuse shell part by forming a composite part while supporting the outer shell for a fine look and drape.
When considering thread density of variable count as needed for the weight or stiffness for a specific use, woven interlinings are made of vastly 100% cotton.
The shrinkage problem is widely noticeable in cotton fabric. So, nowadays poly-cotton blends or PC blends are applied to overcome such problems. Controlling warp and weft combinations like viscose rayon, textured polyester, and wool fabric is also a way to prevent shrinkage.
2. Knitted interlinings
Knitted fabrics have addressed some of the major disadvantages of woven properties regarding lightweight, flexibility, and soft handles in terms of making interlinings.
Due to variations of loop structures in knitted fabrics, it adequately imparts flexibility or making more stretchable together with the volume and stability. Textured filaments used in knitted fabrics help to keep a soft hand feel and also retain its lightweight properties. It is more expensive than its counterpart cotton. It is used in highly fashionable blazers, blouses, etc.
3. Non-woven interlinings
It is made directly from the fiber to the fabric stage in the process without the involvement of any yarn. Reducing the cost of base fabric is a major concern in this fabric.
As nonwoven mainly lacks in strength needed for apparel use, there are many techniques developed to impart the required strength to nonwoven textiles, called Bonding. The common manufacturing technique is to make layers of synthetic fibers. Nonwovens are available from 10 GSM to 200 GSM or above which offers a large range of mechanical properties like light, soft, flexible and for so many applications.
Interlinings can be categorized into two types based on their application point:
- Fusible interlining
- Non-fusible interlining
1. Fusible interlining
Interlining is commonly used as a thermoplastic resin to attach the face fabric by applying heat and pressure for a certain period. It is also known as an adhesive or fusible interlining. Generally, 165-170°C temperature is suitable for fusing.

There are several functions of fusible interlining in garments including stability in shell fabric, controlled volume due to good formability, shape retention of garment by repeated dry cleaning process, appropriate flexibility, enhanced look as well as easy manufacturing of garments. Fused interlining shows excellent adaptability while using and doesn’t create any bubbling effect after washing.
2. Non-fusible interlining or Sewn interlining
Non-fusible interlining is an additional layer placed between the outer fabric and the regular lining of a garment by sewing.
At first, only woven materials were widely used as interlining in apparel but with the growing developments in the textile and fashion industry worldwide, knitted and non-woven interlinings hold a major success these days.
The methods of attaching non-fusible interfacing completely differ from fusible interfacing. Pattern making for interlining to cutting with seam allowances and stitching to adhere are parts of the methodology. Starch solution is applied on the surface of a fabric followed by a drying process for the preparation of sewn interlining and finally sewn with the main fabric. So, proper selection and techniques of attaching interlining to the garments are crucial for quality and aesthetics.
Application of Interlining
Interlining is generally used in collar, cuffs, waist band, front facing of coat, etc.The application of Interlining can be seen various garments:

- Shirts
- Men’s wear and women’s wear
- Coats and trousers
- Suits and jackets
- Casual wear and denim
- Workwear and innerwear
- Accessories
- Deco
- Blouses and dresses
- Knitwear and sportswear
- Lace and embroidery
Importance of Interlining in Garments?
During the manufacturing process, Interlining is placed between the outer fabric and the inner lining attached by heat and pressure. There are so many reasons why interlining is significant for garments.
Structure and Resilience:
An improved structure of interlining not only adds stability to the garment, but also increases its longevity, allowing the garment to retain its shape for longer duration. Besides, an interlining support the required garment while controlling the shape.
Fit and Comfort:
A perfect selection of interlining allows garments to fit the body better, improving the overall fit of a human body.
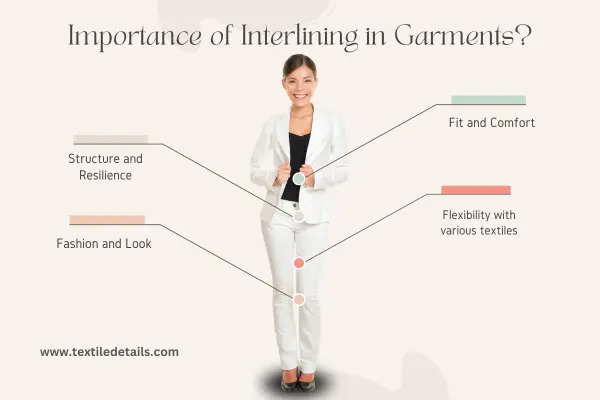
By preventing unwanted creases around the collar and cuffs, ensuring that the garment remains comfortable even after a long day’s wear.
Fashion and Look:
Even though interlining is often hidden between layers of fabric, its characteristics are noticeable in the appearance of the shirt. It’s possible to get a polished and structured appearance by choosing a quality interlining. Different types of interlining can be used to achieve specific effects and also helps to keep a formal look.
Flexibility with various textiles:
Interlining differs with fabrics style, structure and and also purpose. The flexibility and functionality of a fabric can be affected by a wrong selection of interlining.
To reinforce the components of the garment, making the apparel more eye-catching, wearable and attractive and quietly ensuring the anticipated look, quality of the apparel, interning is eminent for the garment manufacturing.
Reference:
- A K Choudhary, Sheena Bansal. Fiber2Fashion. Interlining in apparel manufacture. [ Internet ]. May, 2007. [Cited by 2024, April 22]. Available from:https://www.fibre2fashion.com/industry-article/7928/interlining-in-apparel-manufacture
- Prasanta Sarkar. Online Clothing Study. Different Types of interlining and interlining selection. [ Internet]. September 25, 2018. [ Cited by 2024, April 22 ]. Available from:https://www.onlineclothingstudy.com/2018/09/different-types-of-interlining-and.html?m=1